1000M, The Last Building Designed by Jahn, Rises
ENR Midwest – The 74-story building is Helmut Jahn’s last design
A cantilever creates a dramatic sculptural effect at the 1000M residential tower in Chicago’s South Loop—the last design of the late architect Helmut Jahn. The cantilever at 1000 S. Michigan Avenue swoops over an adjacent, shorter building and makes the most of limited space.
“The cantilever allowed the project developer to capture all of the entitled buildable area,” says David Fields, senior principal for Seattle-based Magnusson Klemencic Associates, the project engineer. “It allows 100% of the added area to go directly into leasable units.”
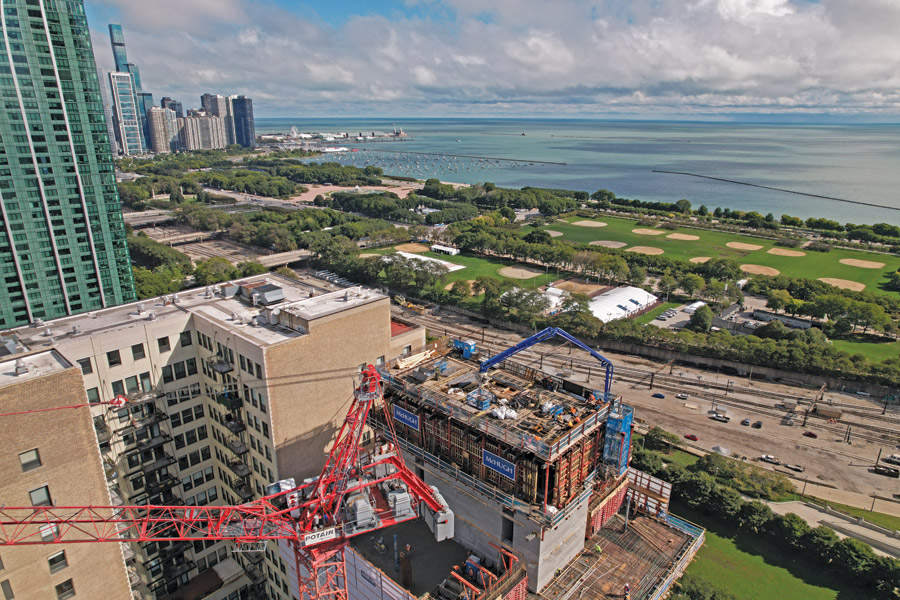
Another goal of the cantilever was to maximize views of Lake Michigan and Grant Park and to get a north-south orientation for the tower. “1006 S. Michigan was part of the assembled property for the planned development, and this allowed us to take advantage of the airspace over the adjacent building,” says Philip Castillo, architect and managing director at Jahn, whose namesake principal died in 2021.
Jahn took a two-volume approach to the tower’s design, creating a rectangular base and a carved tower that widens as it rises.
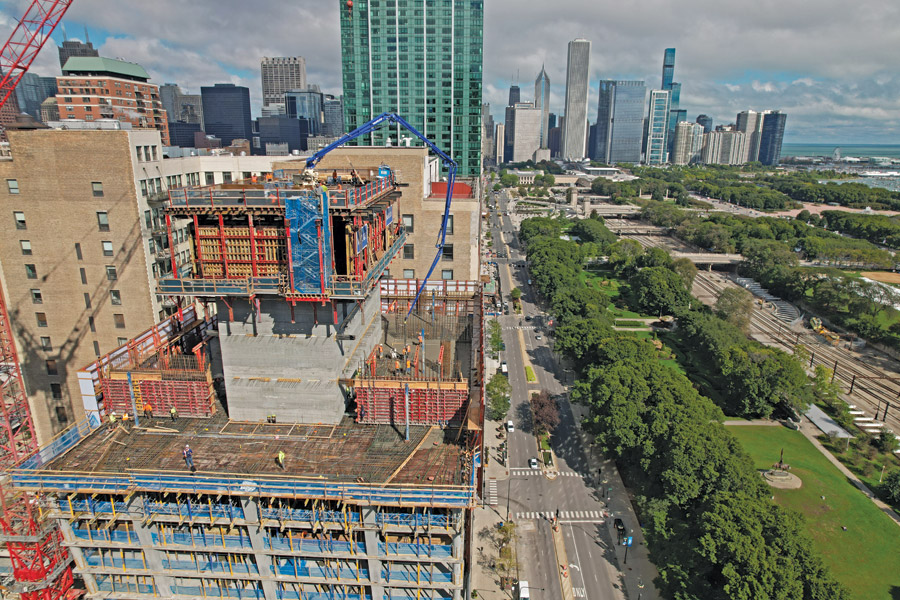
The design and construction team on the 74-story skyscraper had to reconfigure the building from condos to apartments following the COVID-19 pandemic and in response to the evolving real estate market.
Jahn reduced the building’s height by 27 ft and changed it to 738 apartments rather than the 506 condominiums it was originally planned for. Under the new design, the building fronting Michigan Avenue will still be Jahn’s tallest in Chicago, at 805 ft, rather than 832 ft in the original plans.
“A more conventional approach, prismatically extending the building taller, could have added the same area, but much of it would have been taken up by additional elevator, stair, corridor and other unsalable spaces,” Fields says.
The cantilever was created by a series of sloping columns along the south face of the building from Level 11 to 20.

“The biggest engineering obstacle from a design perspective was resolving the forces imposed by the cantilevered levels,” Castillo says.
“This geometry [of the cantilever] induces major lateral forces on the building, not unlike the horizontal forces felt during a windstorm,” Fields explains. “The challenge was to provide stability for these columns and resist the lateral forces with the same structural system that resists the wind forces.”
The building’s overall lateral stability is ensured by a concrete shear wall core and buttress wall system, Fields says. The sloping columns at the south cantilever are tied back to the shear wall system via heavy bands of high-strength reinforcement in the adjoining slabs.
The heavy bands take up a large volume within the slabs and compete for space in the grid of post-tensioning tendons.
The construction team addressed these issues in a preconstruction conference “where the construction challenges were discussed and best ideas expressed,” Fields says. “A full-size mock-up was created to verify these elements could all be placed within a very tight area while maintaining the necessary configuration.”
The installation of the cantilever was observed on site by MKA to verify the final placement and to resolve any unexpected conflicts.
Changing from condos to apartments created other challenges, including alterations needed for the mechanical, electrical and plumbing systems.
“When the project shifted from condos to apartments, it required a coordinated redevelopment of the MEP design-build system,” says David Steffenhagen, senior project manager at McHugh Construction. “The unit sizes and quantities were changed, and the MEP requirements for apartments are different than condos from an MEP standpoint.”
Castillo says the shift to apartments also prompted the need for more amenities, which generally are a larger program element in a rental than a condo building.
“It required a coordinated redevelopment of the MEP design-build system.”
David Steffenhagen, Senior Project Manager, McHugh Construction
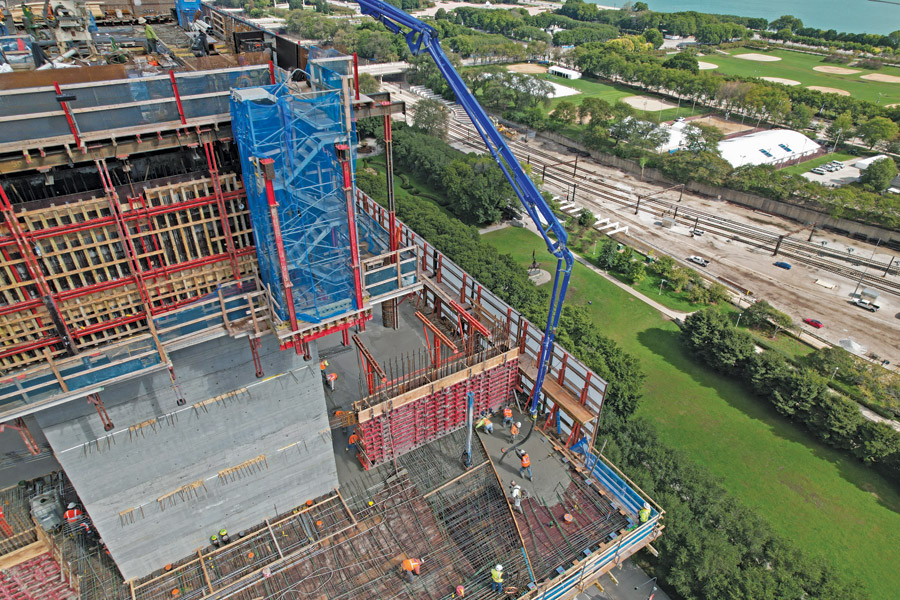
The building design was adapted to feature 70,000 sq ft of amenities space, including a resident lounge and shared demonstration kitchen, an art gallery, a fitness center and an indoor pool and spa overlooking an outdoor pool deck.
Jahn lowered the ceiling heights of rental units to 9 ft, which allowed more amenity floors with higher ceilings. Amenities are on seven floors of the building.
MKA planned for a thickened slab at Level 10, tied the structure back to the core and created a platform to support the sloping floors from floors 10 through 19, Castillo says.
Another challenge involved installing the curtain wall.
“From a construction standpoint, one of the biggest challenges was coordinating tower crane tie-ins with curtain wall installation,” Steffenhagen says. “Earlier in 2022, we coordinated the tower crane tie-ins with the vertical mullions and window locations. This ensured that the curtain wall would be installed above the tie-in location.”
“The coordination process includes determining where a crane tie-in must occur followed up by what part of the window system can be left out to allow the tie-in to pass through,” Steffenhagen says. “The crane tie-in is used to support the tower crane during construction.”
Communication throughout the project was the key to success. “It takes a lot of meetings with designers and engineers to prove both systems can work together. The fruits of this labor are realized when the windows are installed and the fractions of inches shown on paper can be measured in the field,” Steffenhagen says.
He said that the curtain wall system stacks from floor to floor, so it is not possible to skip a floor.
“Coordination is critical because it allows us to enclose the building around the tie-ins and complete the finishes in those units to achieve unit turnover on schedule,” he says.
Another coordination issue was the design and installation of the curtain wall system on the negative slope area of the building, where it cantilevers over the neighboring building.
Coordinating the column and slab edge locations with the curtain wall embeds was a delicate operation that required precision.
“Columns must be located within the structural design tolerances, and window embeds have to be located per the curtain wall structural design,” Steffenhagen says. “Special care had to be taken while placing the window embeds within the slab to ensure all the embeds lined up floor to floor.”
The building’s location in the historic district presented another challenge since zoning does not allow curb cuts along Michigan Avenue.
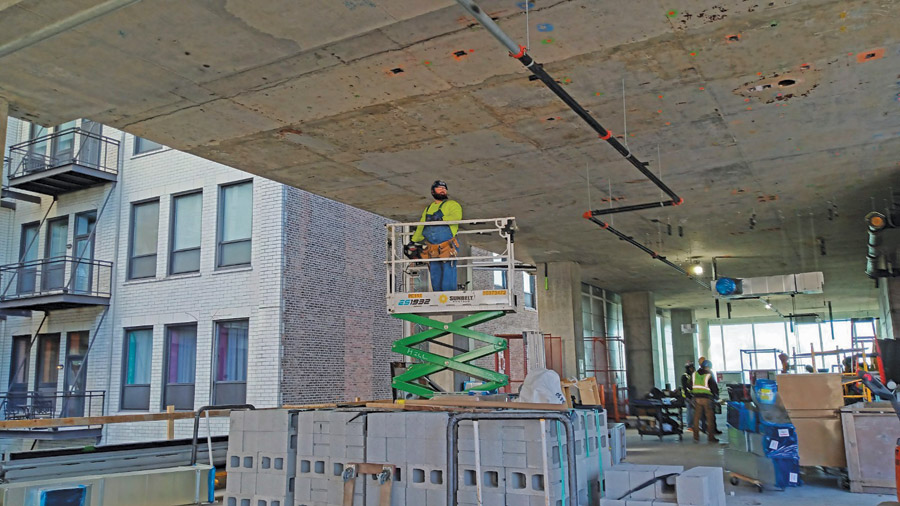
Jahn utilized a small parcel along Wabash Avenue that was also part of the planned development.
“This allowed planning for a porte cochere that, in turn, provided a dignified vehicular entrance and a second lobby, which will be an important entrance to the building,” Castillo says.
Having the Wabash Avenue entrance also was a plus during construction.
“Our team needs to be able to move a massive amount of material into the building on a daily basis, and trucks need to be unloaded and materials distributed quickly,” Steffenhagen says. “From Day 1, we developed our logistics plan to avoid using Michigan Avenue.”
While 1000M presented its own unique challenges, the team also coped with other issues affecting the entire industry.
“The supply chain in the post-COVID world remains a challenge, so when materials are ordered, you cannot depend on them showing up on time,” Steffenhagen says. “Our entire approach to the buyout of the building was to thoroughly interview subcontractors and vendors and get approvals and orders early.”
They also visited manufacturing plants to make sure materials were being made on time and to specifications.
“We have found that vendors who relied heavily on outsourcing their materials or manufacturing were often not reliable or competitive. Sometimes it’s worth a plane trip to investigate and verify,” Steffenhagen says.
While the change from condos to apartments required team members to think fast on their feet and turn around a new design quickly, Castillo says the result has been positive and still respects the original design concept envisioned by Helmut Jahn.
“For the public, looking at 1000M from Grant Park dramatically reveals the sculptural cantilever form as envisioned by Jahn.”
David Fields Senior Principal, MKA
“The change in program allowed us to rethink the lobby and entry sequence as well as simplify the top of the tower,” Castillo says. “All in all, the changes resulted in a stronger architectural statement and a better building.”
Fields predicts the cantilever will be appreciated by the public. “Looking at 1000M from Grant Park dramatically reveals the sculptural cantilever form as envisioned by Jahn,” he says.
“For the structural engineer, satisfaction is taken in the knowledge that it is equally an expression of raw physics and then teamwork between engineering and construction teams to make this form a reality,” he says.”
Topping out is slated for summer; partial occupancy is expected in early 2024, with final completion in late summer 2024.